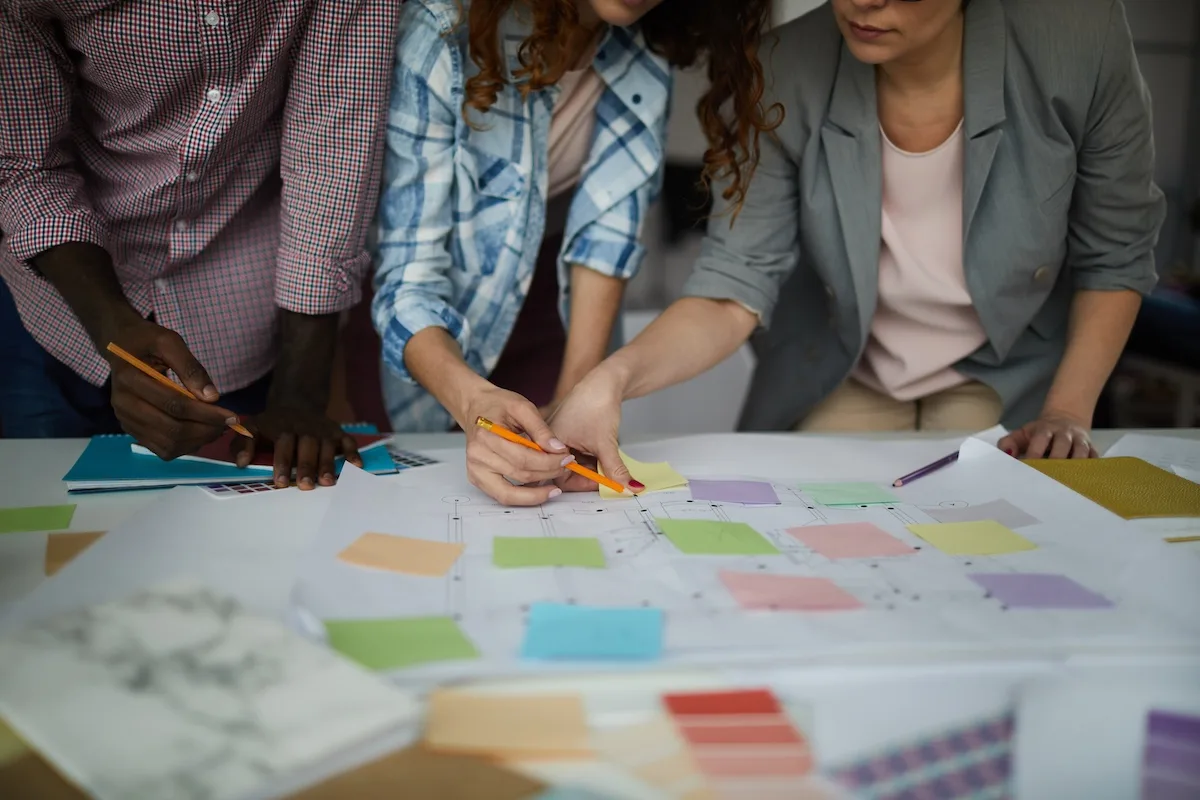
Fundamentals
of Operational
Excellence #4:
Use a Process-Based
Framework for Key Decisions
Summary
- our system should be made up of a set of processes necessary to manage the risks within the scope
- A process-based system has less built-in complexity, can have embedded continuous improvement, and is easier to manage through design and implementation
- A process-based system is a good way to avoid building your system around and reinforcing, existing organizational silos
So far, we’ve looked at several factors for Operational Excellence, specifically related to your management system. We’ve established the need to have: an integrated system, a system that allows you to remain agile, and a system designed specifically for your needs.
This article dives a little deeper into how you should structure your management system framework to avoid introducing much of the complexity that inhibits progress through a Process-Based Framework.
The focal point of your management system
is improving your decisions
Think about any important decision you make. Be it a decision to hire a new candidate, a decision about whether to invest in a new product idea, or a decision to shut down a piece of equipment to perform an inspection, each key decision will have some impact on how consistently and efficiently your company executes its strategy. Even day-to-day decisions about how to prioritize our time add up and impact overall performance.
Behind each of these decisions, there is usually a process. In some companies, that process varies depending on who is making the decision. In smaller companies, the process is simply to ask the boss. In all cases, there is a process being followed with the intention of making the best decision. A management system can, therefore, be simplified down to a set of interrelated processes that, when working together, will yield better decisions.
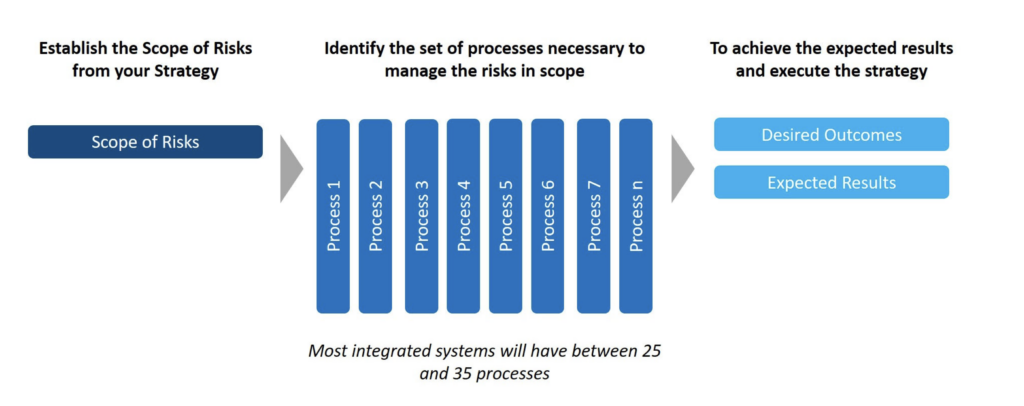
3 Benefits of a Process-Based Framework Approach
1. Arranging the system as a set of distinct processes helps identify overlap or potential conflicts in decision-making
Many integrated systems suffer from built-in complexity because they are made up of a combination of processes, outcomes and things. For example, in developing a car, imagine you gave one group responsibility for vehicle safety, another group responsibility for hydraulic systems, and another group responsibility for stopping the vehicle. What group makes decisions regarding the brakes? On a relatively simple project like a car, it would be easy to identify this interdependency between the three groups, but in large complex organizations, this overlap is easily buried.
We see this often with systems that have elements such as “Asset Integrity”, “Safety”, or “Quality”. These are outcomes that all rely on the same set of processes, so what ends up happening is redundant and even contradictory controls get put in place. For example, a mid-sized Oil and Gas company was having issues with repeat incidents related to operating a critical piece of equipment. Despite the usual corrective action efforts like offering more training and improving warning signage, the issues remained. Eventually, they realized that, depending on several factors, an operator could end up using one of 7 different instructions, each created by a different group that had something to say about that equipment.
The most efficient systems start with the risks to achieving the desired outcomes and expected results, and from that, they identify the unique processes necessary to fully address the risks without creating duplication, overlap, or conflicts.
2. Building the system as a set of processes makes embedding continuous improvement much easier
Processes are much easier than outcomes to break down into their inputs, outputs, and discrete repeatable steps. You can identify a clear objective and scope for each and observe if the process is being followed. These are the basics of Deming’s system for continuous improvement. By structuring your system as a set of processes, you can drill down to the individual processes that may be failing and contributing to the overall system’s performance.
3. A process-based approach will make development more manageable
Process-based systems are easier to sequence and prioritize for development. Since processes have inputs and outputs, you can understand their dependencies and thus break up the development into more manageable sections. This has big implications for deployment, as the system can be piloted and refined, thus improving adoption, rather than relying on a big-bang deployment.
Using a process-based approach seems logical yet all too often, companies fall for the same trap of embedding outcomes and things into their system. Usually, this is driven by the desire of senior executives to see certain keywords present as if to make them seem more important or to reinforce existing organizational division of responsibilities by function.
This is an important junction in the road – the system will either reinforce existing silos and politics, or it will move the organization beyond them. A small change in the foundational design of the system can have large-scale implications for its effectiveness and efficiency, so be very weary of compromising the system’s design at this point.
Where to begin
Taking a process-based approach introduces several challenges. What processes are necessary to manage the scope of risks? How do you know you have all the processes you need to manage your company and remain compliant with all necessary regulations, while not creating redundancy and waste? Where are the dependencies between them?
Endeavor Management provides its clients with a world-class Integrated Management System that can be tailored to their organizational needs and regulatory/industry requirements. Our system can quickly identify the processes you need to manage your risks and remain compliant with all regulatory or industry requirements. For more information on the Endeavor Management Integrated Management System, contact us and one of our Management System experts will guide you through the process.
Designing the System for your Needs
Keeping it Simple
This post is an excerpt from the white paper “The Fundamentals for Transforming Your Organization Through Operational Excellence.”
Let’s Talk
We will help you overcome strategic challenges to realize the business value you seek.