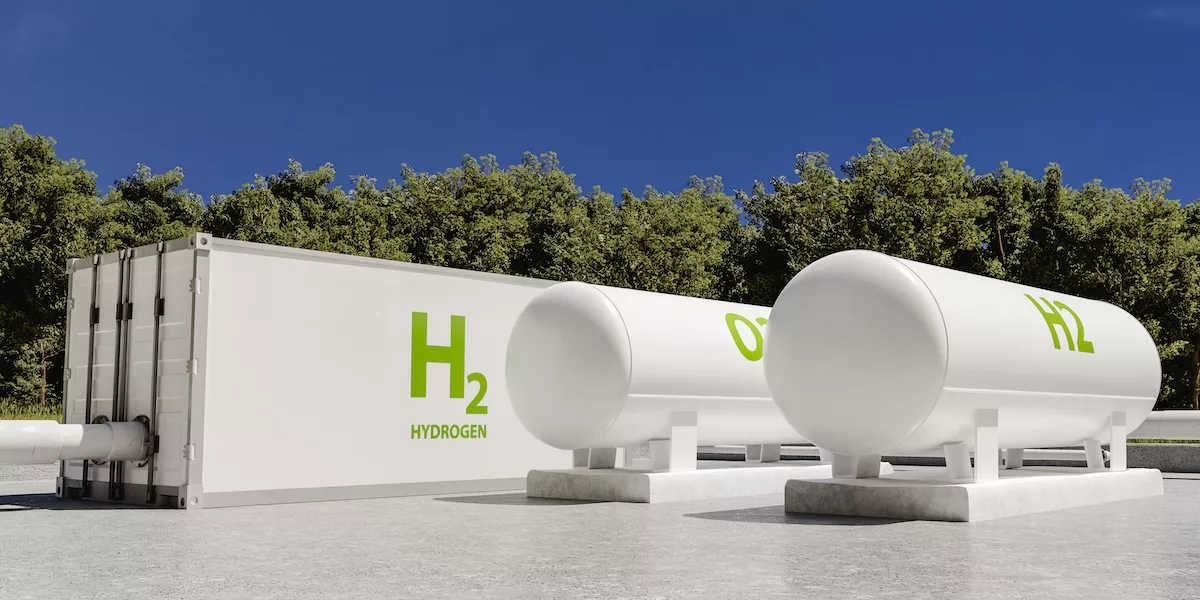
Hydrogen
Storage Options
In this the fourth of five short blogs, we will address, again without going deeply into the weeds, the options for the storage of hydrogen. Hydrogen can be stored as a gas at high pressures or as a liquid at very low temperatures or in the form of a liquid hydrogen carrier e.g., ammonia or liquid organic hydrogen carrier (LOHC).
As a Compressed Gas Underground
To smooth out production from green hydrogen production it has been proposed that hydrogen can be stored in vast quantities in underground storage salt domes, hard rock caverns, abandoned oil and gas wells and saline aquifers. From this storage it can be dispatched via pipelines to end users e.g., fuel cells to make electricity, industrial users, etc. The feasibility of storage in salt domes has been commercially demonstrated at five sites in the United States, United Kingdom and Germany with all supplying hydrogen to petrochemical operations. Although saline aquifers and depleted oil and gas fields are used for natural gas storage, they have not been used for hydrogen storage. Issues such as available storage locations near the point of hydrogen production, leakage, suitable geology not universally available, etc. will require addressing.
As a Compressed Gas in Pressurized Tubes
The reader is referred to the discussion in our previous Blog 03 – “Hydrogen – Transportation Options” about the truck transportation of compressed hydrogen.
As a Liquid
While liquid hydrogen has a higher energy density than compressed hydrogen, more energy is required to liquify hydrogen than for compressing it, e.g., about 30% of its lower heating value (LHV) is needed. This compared to about 10% of its LHV for methane. Hydrogen, which liquifies at -423 °F, requires an expensive liquefier plant and a spherical vacuum insulated tank (sometimes call a Dewar tank). NASA operates a 34 MTPD (metric ton per day) liquefaction facility for rocket fuel which is about 10% of the world’s total hydrogen liquefaction capacity and stores it in two of the world’s largest spherical tanks each having the capacity of about 225 MT. Hydrogen boil-off from liquid storage must not be vented because of its green-house gas potential and needs to be either be re-liquefied or burned.
As Ammonia
As discussed in our previous Blog 3 – “Hydrogen Transport Options – Ammonia as Carrier”, ammonia can be stored as a liquid at low pressure 250 psi tanks or in cryogenic tanks at -27 F at 14.7 psi. It can readily be dispatched from these tanks to a user where it can either be decomposed and processed to a pure hydrogen stream or directly burned. Large scale refrigerated (cryogenic) ammonia storage is widely practiced at ammonia production facilities throughout the world. Typical tank size is in the range of 15,000 to 30,000 MT with many sites having multiple tanks. The two largest tanks, 50,000 MT each, built by the Qatar Fertilizer Company (QAFCO), are in Mesaieed, Qatar.
As a Liquid Organic Hydrogen Carrier (LOHC)
As discussed in our previous Blog 3 “Hydrogen Transport Options”, LOHC’s can be stored in atmospheric, non-refrigerated tanks like those used for gasoline or other liquid hydrocarbon fuels. It can be dispatched from the tank to be decomposed to hydrogen and with the carrier being returned to react with fresh hydrogen at the point of the original hydrogen production. Very large-scale hydrocarbon storage of this type is widely practiced throughout the world.
Compared to ammonia, LOHC’s are easier to handle, store and transport because they are similar to gasoline. They can use existing hydrocarbon transportation infrastructure such as tankers, trucks, pipelines, and tanks. As noted in our earlier blog, LOCH has been demonstrated only at a very limited scale.
Let’s Talk
We will help you overcome strategic challenges to realize the business value you seek.