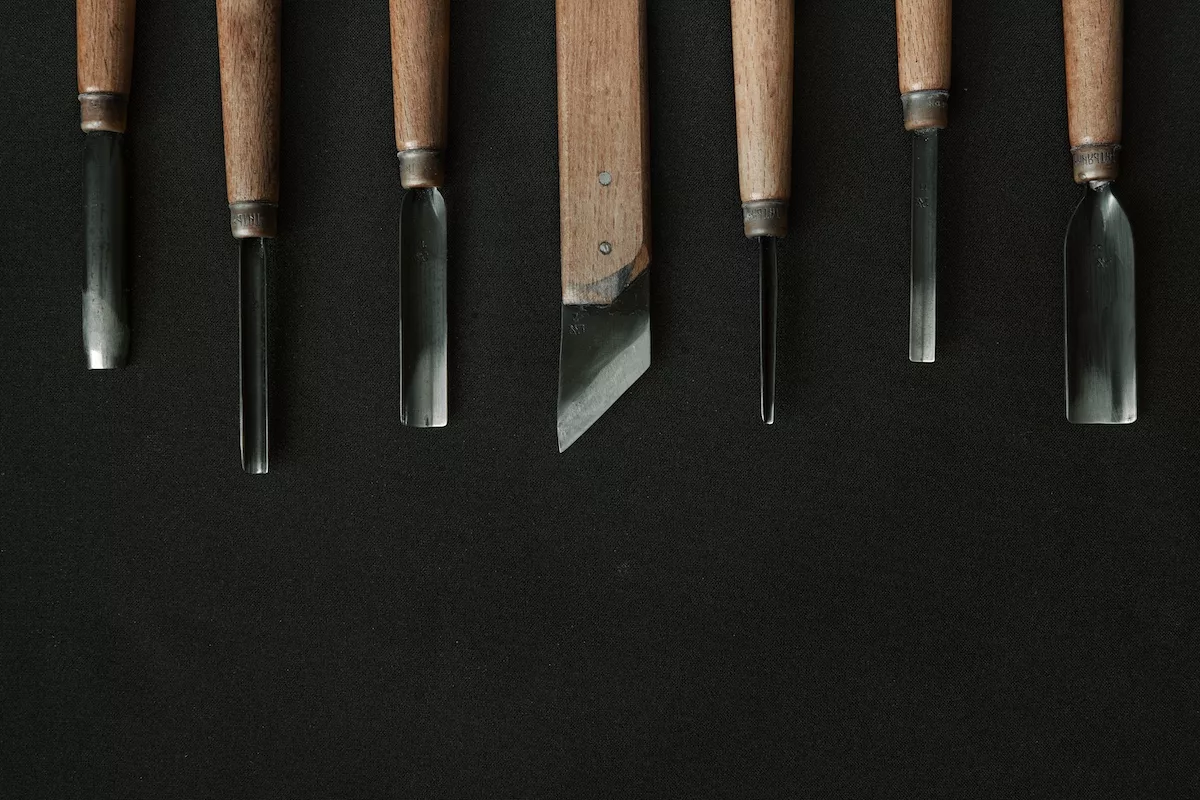
Lean Six Sigma:
Where does it fit within Operational Excellence?
Same Tools, Different Names?
There seems to be a lot of noise and general misconceptions about Lean Six Sigma (LSS) and Operational Excellence (OE). Are they different terms for the same thing? Are they just different approaches to the same end goal? If they are different, which one is right for me?
This is not an inconsequential topic since both are considered approaches to Continuous Improvement (CI). Studies have found over half of executives say their CI programs have failed to produce the expected results and over 2/3 say their programs need to be changed or reconsidered. Without clear expectations, both on the expected benefits and the required investment and organizational commitment to make them work, expectations can easily be missed. Avoiding this requires having a clear idea of the difference between alternative approaches to CI and why some work in some situations but not others.
Similarities
It is easy to see why many people see LSS and OE as essentially the same thing. On the surface, they have many similarities. They are both based on the same fundamental principles of taking a systematic approach to continuous improvement. They both result in standardization of processes, they both look to address risk and they both incorporate some aspect of culture that is necessary for success.
From the outside looking in, they seem very similar, but this is where the similarities end. When you look at the scope of what they are seeking to accomplish and the specific approach they require, they are completely different.
LSS & OE have many similarities, though they differ greatly in their scope and approach
Lean Six Sigma | Similarities | Operational Excellence |
---|---|---|
The LSS tools and methodologies are designed to work as a system | Use a systematic approach | All processes, equipment, and people in the organization are viewed as a system |
Standardize the Value Chain process | Improvement through standardized processes | Standardize the Management System process |
LSS designed to be an ongoing system of refining the Value Chain | Based on PDCA cycle of CI | Ongoing system to improve overall decision-making across organization |
Remove waste and align customer value expectations | Look to address risks | Address risks to achieving mission and vision, including cost, quality, HSE, etc. |
Lean mentality encourages all employees to be vigilant of waste | Incorporate “mentality” or “culture” | Focuses on the overall culture of the organization for better decision making |
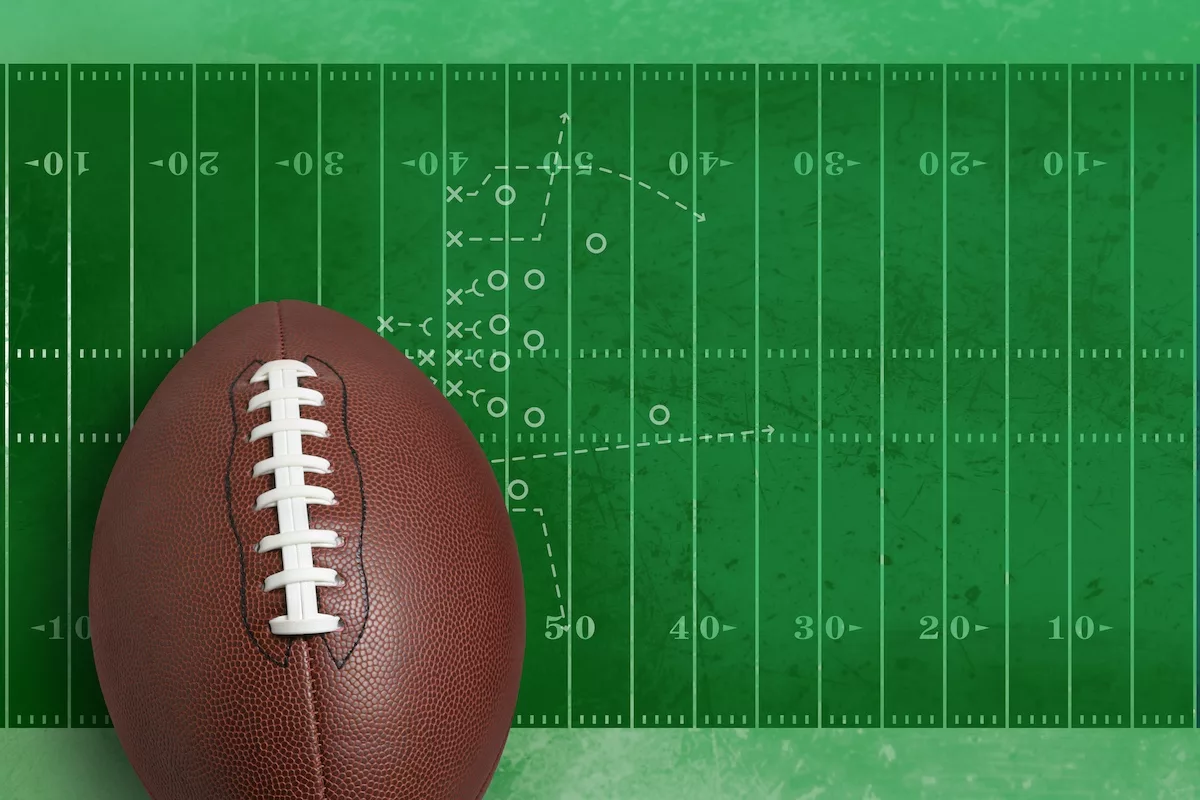
LSS vs. OE
in Football
A simple analogy can be found in football. Taking a LSS approach is like taking an individual play, assessing its performance, and refining it to address its weaknesses over time.
OE requires a different approach. It stars with the overall stratey and vision for the team and looks at how that vision and strategy translates to every decision made by the team. From how the coaching staff makes decisions about team members, positions, and play calls, to how the player’s behavior impacts the overall appeal of the team with the fans, how to better leverage merchandising, advertising and marketing, and how everything works.
Key Differences
Overall, the key difference between the two is the scope of what they consider the “system”. With LSS, the system is usually a single process within the overall value chain, whereas Operational Excellence is not possible without looking at the entire organization as a system. LSS can work very well in the right conditions, but often it runs into two critical limitations.
LSS Limitation #1: Problems Outside the “System”
A LSS program can result in a world-class set of Standard Work Processes, but if any of the systems for hiring the right staff, for documenting the standards, for training or for rewarding workers for following the process are broken, the standards will not lead to sustainable improved performance.
LSS Limitation #2: Inadvertent Negative Impacts
Any process within the business can have an indirect impact on seemingly unrelated processes. What can seem like waste within that process may be enabling agility or efficiency elsewhere. This is a natural limitation of bottom-up approaches like LSS, and even temporary improvements may lead to negative long-term impacts to the overall system.
Operational Excellence requires a different approach – one that starts with the overall strategy and vision for the organization and ensures alignment across all decisions on how to meet that vision and execute the strategy. This includes aligning how the organization identifies, assesses and prioritizes risks, whether the risk is to product quality and customer value, to the overall growth targets of the business, to the health and safety of employees and stakeholders, to the environment, or to anything else that the organization values.
Lean Six Sigma and Operational Excellence are not the same thing, but they are also not incompatible. LSS has been proven to be successful in many applications, but it has several limitations absent something to align the broader organization. Operational Excellence can deliver tremendous sustained value by creating greater alignment across the organization, but it still relies on the proper application of tools like LSS to unlock value where needed. When LSS becomes a part of the overall journey toward Operational Excellence, the value of both programs is amplified.
Lean Six Sigma | Operational Excellence | |
---|---|---|
Bottom-up: Focused on individual processes | Overall Approach | Top-down: Focused on the overall business |
Enhance customer value | Objectives | Consistent and reliable execution of the strategy in alignment with the mission and vision |
Cost, Lead-time, Quality | Success Measures | Revenue, profitability, growth, safety, environmental performance, employee retention |
– Well-known processes – Wide Variety of tools available – Faster ROI | Benefits | – Transformative results impacting whole business – Holistic view of the business – Long-term results |
– Quickly addressing problematic processes in targeted ways – Industries with low volatility – Companies with very similar, low variability processes | Best For | – Driving sustained transformation over long-term – High volatile industries – Companies with differentiated businesses and needs |
Let’s Talk
We will help you overcome strategic challenges to realize the business value you seek.